Thermal Spraying Technology R&D Laboratories
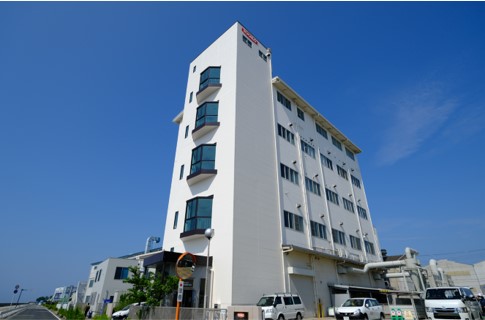
R&D vision
The Thermal Spraying Technology R&D Laboratories follow R&D policies based on the TOCALO Management Policy. We actively pursue various research themes following our four perspectives and flexibly modify our organization and structure to develop innovative functional coatings that will contribute to future technologies.
75th Term R&D basic policies
- Develop advanced coatings
Focus on the aerospace and semiconductor field, and strengthen the intellectual property strategy - Reduce environmental impact
Develop initiatives aimed at providing Good Service - Increase manufacturing sophistication
Actively use machine learning and computational science - Cultivate diverse human resources
Cultivate human resources and eagerly pursue advanced technologies
Core technology
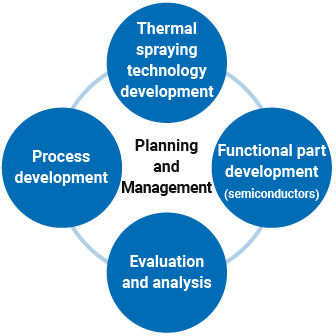
Thermal spraying technology
The thermal spraying process, particularly plasma and high-speed flame thermal spraying, is currently used in wide range of industries, including the environmental, energy, industrial machinery, and medical industries. Current development of the thermal spraying process is focusing primarily on improving the functionality of the coating characteristics by atomizing the coating materials to control the coating structure and by using high-speed particle spraying to increase coating density.
Monitoring the speed and temperature of the coating spray will enable us to optimize the spray powder and coating conditions leading to new levels of high-functional coating that are beyond the ability of current technologies. We are also anticipating a trend in the future of growing demand for technology that will lower the environmental impact of thermal spraying processes, and we are accordingly seeking to develop technology that meets the needs of society and our customers.
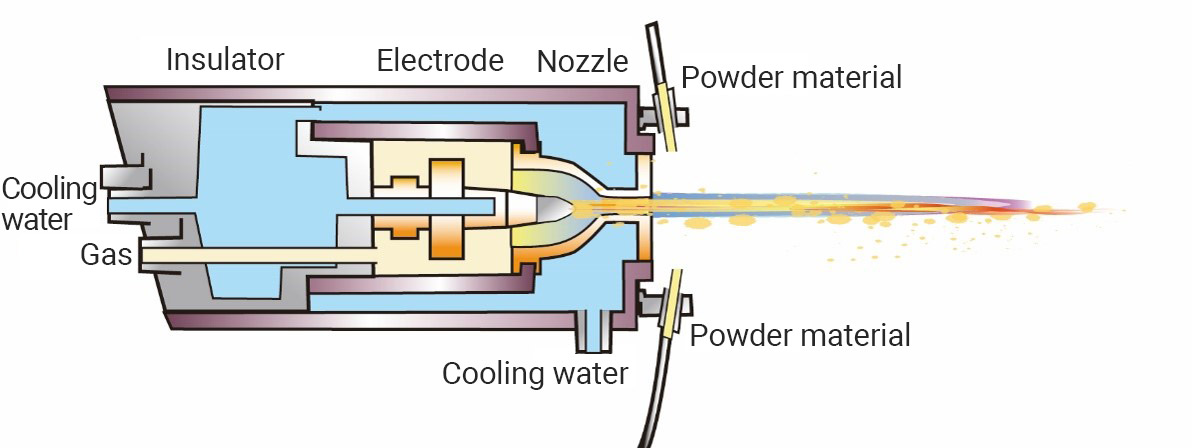
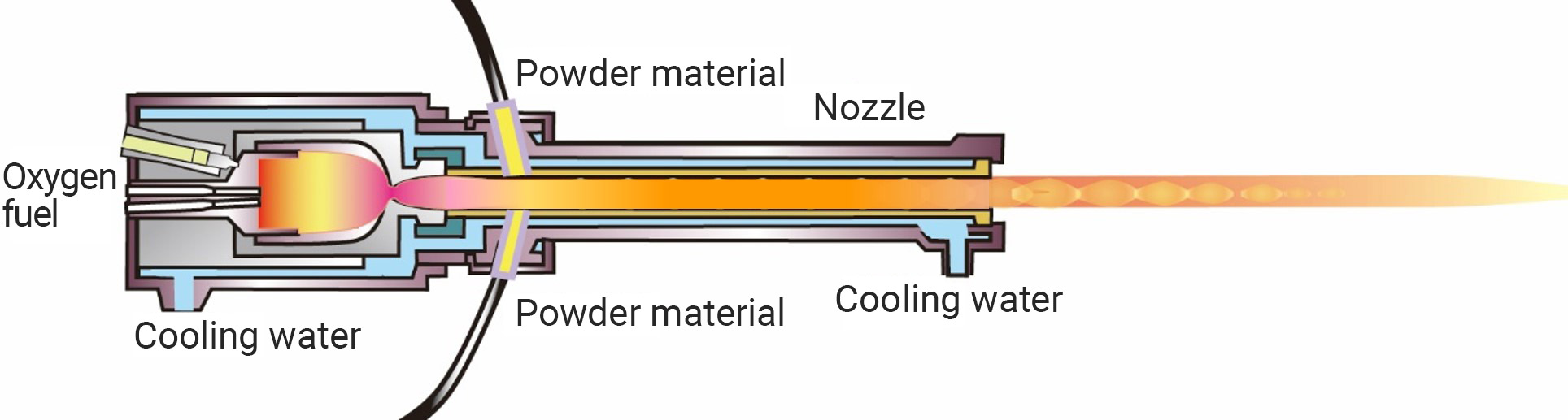
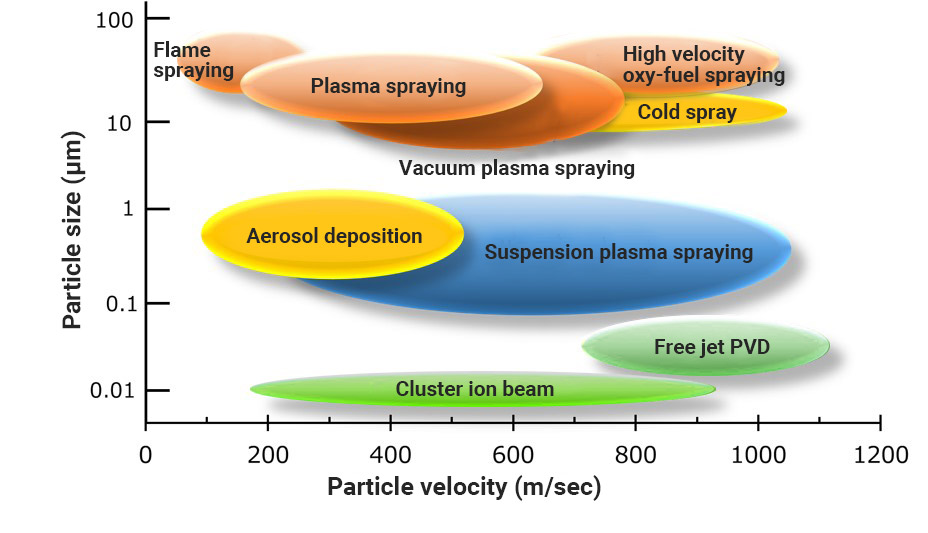
Suspension plasma spraying (SPS, SHVOF)
Suspension spraying is a new thermal spraying method in which the coating material is delivered while suspended in solution making it possible to spray ultrafine particle powder. We are developing coatings specialized for suspension plasma spraying (SPS) and for suspension high velocity oxy-fuel (SHVOF) spraying. By adjusting the spray conditions, using fine particles to form coatings makes it possible to form either a low-porosity, ultra-dense coating with or an ultra-porous coating. The coating can be formulated to different specifications, such as an ultra-dense coating for stronger wear resistance or an ultra-porous coating for enhanced thermal conductivity or catalytic properties. At the Thermal Spraying Technology R&D Laboratories, we are developing coating that use these thermal spraying technologies, evaluating the coating characteristics, and developing applications for the coatings.
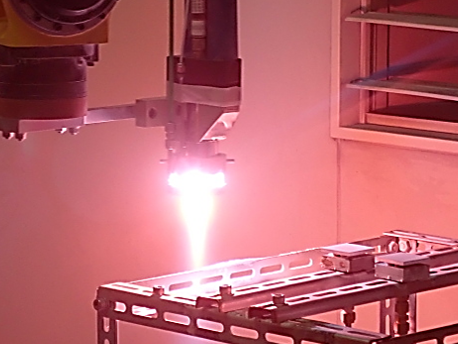
Process development
We are also developing coating processes other than thermal spraying that use chemical reactions or physical effects. One focus of our research is using laser technology in surface modifications and cladding processes, and we are actively evaluating coating characteristics and developing applications. We are also advancing thin coating technologies, such as a physical vapor deposition (PVD) and chemical vapor deposition (CVD), and wet process coating technology that make a wide range of coatings possible, including diamond-like carbon (DLC), ceramic, and specialty resin coatings. We will continue to developing environment-friendly processes and coatings for all types of businesses and industries.
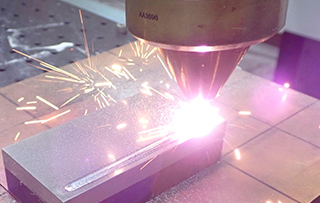
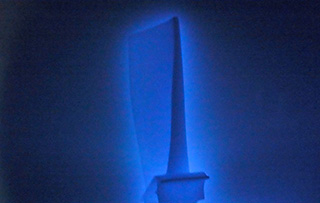
Laser technology (laser cladding)
Laser cladding is an overlay technology using a laser beam as the heat source for forming a coating overlay by depositing powder material to the laser’s focal point where it melts and bonds to the substrate surface. Laser cladding creates less heat input to the substrate than conventional overlay technology, which reduces thermal strain during processing and minimizes substrate dilution into the coating. The technology is also environmentally friendly as it is more power efficient than thermal spraying and increases productivity in the coating formation process. At the Thermal Spraying Technology R&D Laboratories, we are using our laser cladding technology to develop and create applications for functional coatings with excellent corrosion, abrasion, and cavitation resistance.
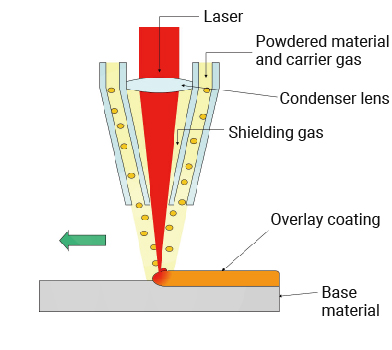
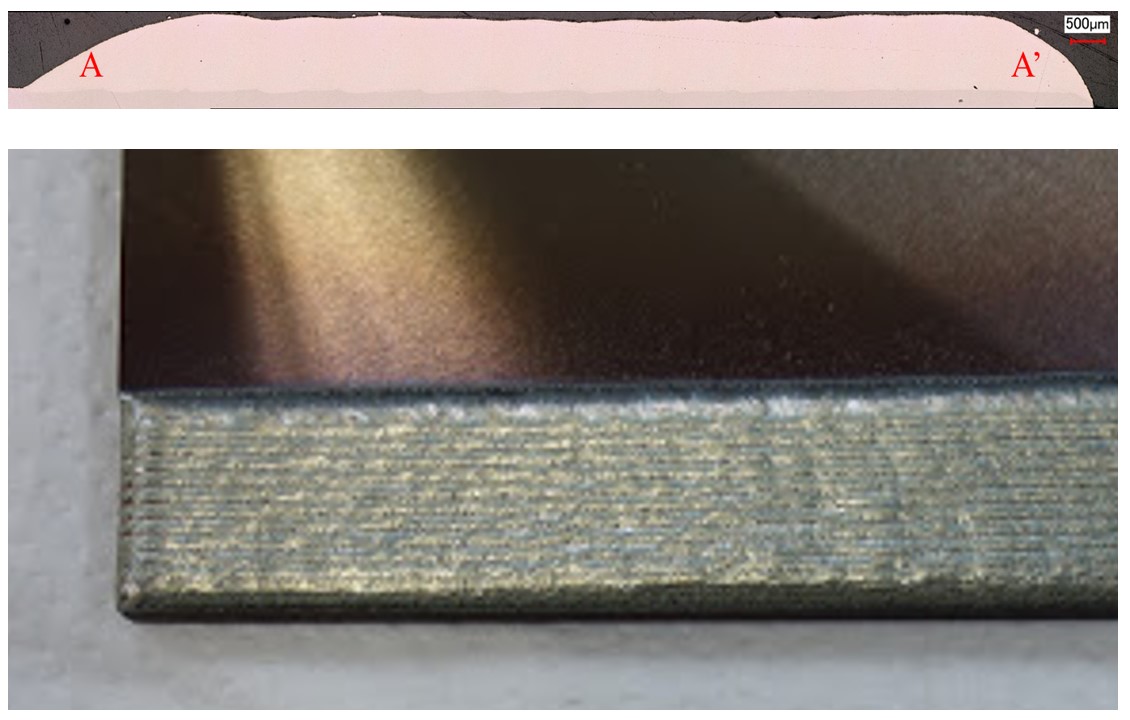
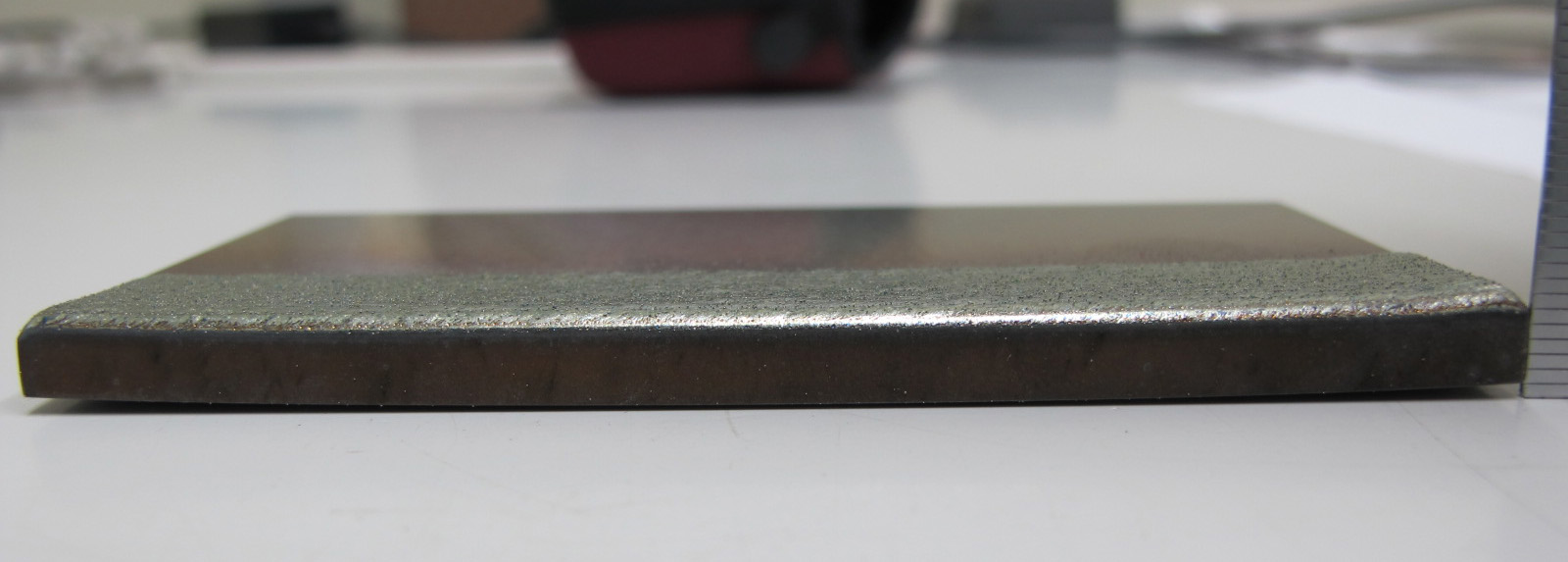
Functional component technology (semiconductor)
Semiconductors are becoming increasingly more scaled while being designed with three-dimensional structures in order to have the capacity to store and process the huge amount of data required by our rapidly expanding information society. The thermal spraying of high-performance coatings on semiconductor manufacturing equipment parts greatly improves the quality and productivity of semiconductor devices.
At the Thermal Spraying Technology R&D Laboratories, we are developing high-functional coatings for semiconductor manufacturing equipment, including ceramic-coated parts to extend the useful life and reduce the dust generation, electrostatic chucks that can hold wafers and control their temperatures, and various parts with heating and temperature measurement functions. We are using computer-aided engineering (CAE) software in our coating design activities from the composition to the heat transfer and liquidity characteristics as we seek to rapidly and efficiently develop products.
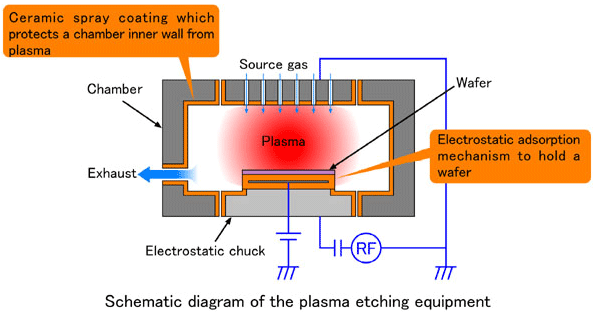
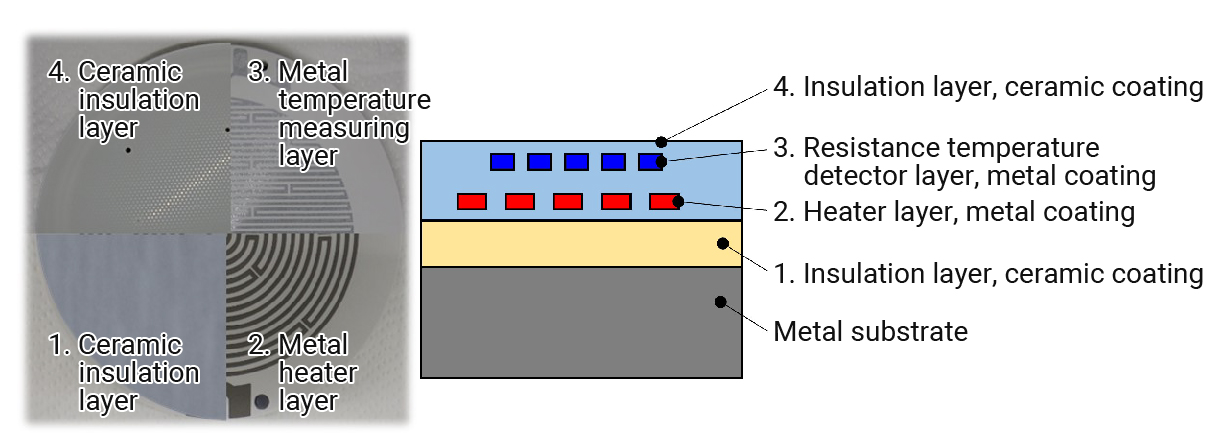
Evaluation and analysis
The Thermal Spraying Technology R&D Laboratories conduct extensive evaluation and analysis of prototype coatings. We develop coatings to meet customer performance specifications, and test the physical properties and conduct analytical evaluations to provide coatings that meet customer requirements. Our analytical evaluations include categories shown in the table, but can also extend to simulation tests using actual machinery and analysis for quality control. We also develop new test methods and testing equipment to better evaluate the physical properties of coatings for suitability not just with existing equipment but to improve how our coatings perform during processing.
Table 1 List of evaluation and analysis categories (example)
Analytical evaluation | Chemical analysis | Energy Dispersive X-ray Analysis (EDS) | |
---|---|---|---|
X-ray diffraction (XRD) / crystal phase identification, thin coating compatibility, RIR quantification | |||
Thermogravimetric and differential thermal analysis (TG-DTA) | |||
Physical analysis | Vickers hardness (HV) measurement, Rockwell hardness | ||
Surface roughness measurement, 3D roughness measurement | |||
Laser particle size analysis | |||
Physical property evaluation | Abrasion resistance | Suga type wear test, friction wear test, rubbing test, Ogoshi type wear test | |
Erosion resistance | High temperature blast erosion test, slurry erosion test, cavitation erosion test | ||
Corrosion resistance | Electrochemical measurement, CASS test, salt spray test, various immersion tests | ||
Adhesion | Adhesion test, scratch test, shear failure test, bending test | ||
Heat-resistance | High temperature holding test, thermal shock test, burner heating test | ||
Texture observation | Microscopic observation |
Scanning electron microscope (SEM, FE-SEM), laser microscope, ion milling, microscope, optical microscope |
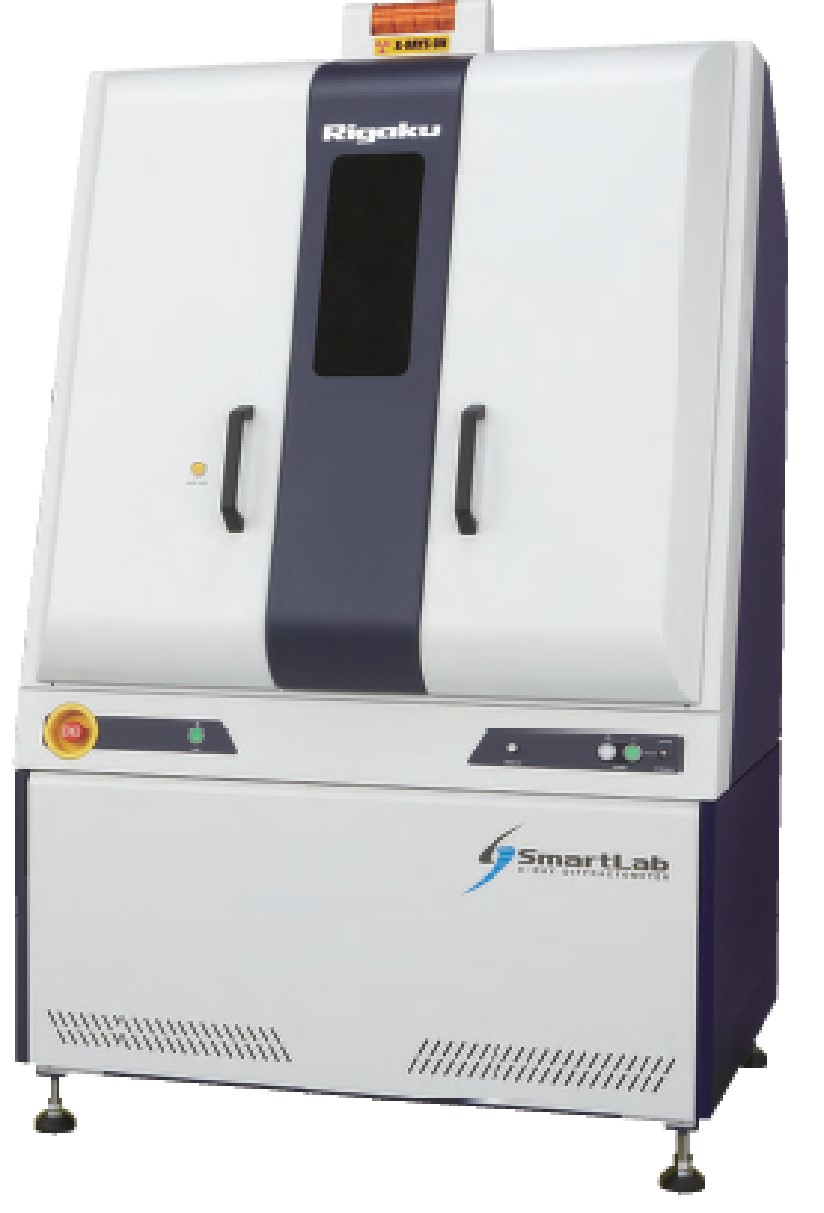
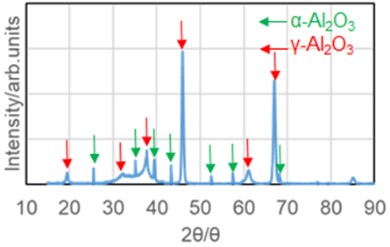